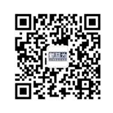
微信公眾號二維碼
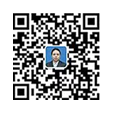
微信咨詢顧問二維碼
新益為品質管理咨詢公司概述:“自下而上的控制、模塊化生長、鼓勵犯錯誤……”熟悉朋友一定知道,這是在《失控》一書中,提出的著名“九律”。只要堅守這九律,就能夠有如神助一般無往而不利。
豐田生產(chǎn)
有意思的是,豐田,這家最傳統(tǒng)、系統(tǒng)結構超級復雜的汽車制造企業(yè),銷量在過去40年里持續(xù)保持增長,并成為全球利潤最高的車企。而豐田公司的管理模式,早已將這種規(guī)律融入到了自己的骨血之中。
豐田精益模式的核心,即為“如何通過自我調整和持續(xù)改善邁向卓越”,不僅僅是告訴制造業(yè)老板們該如何持續(xù)穩(wěn)定地賺錢,保持組織體基業(yè)長青,更是一套教你如何面對商業(yè)世界不確定性的成熟方法論。
這套“通過方法管理”的精益模式,頗值正處在水深火熱之中的中國制造業(yè)老板們,認真體味。
一、要學豐田,看得見的解決方案并不重要
豐田究竟有多牛?下面一組數(shù)字,會帶給你一個直觀的感受:
1、在美國汽車廠商的銷售遇到天花板甚至下降的時候,豐田的銷量在過去40年里持續(xù)保持增長;
2、豐田的利潤超過其他任何一家汽車制造商;
3、豐田的市場資本額已經(jīng)連續(xù)四年超過通用、福特和克萊斯勒,最近幾年甚至超過了它們的總和。
那么,與全球其他大型汽車制造商相比,豐田究竟做對了什么?你究竟該怎樣認知和學習豐田?長久以來,有那么多的人學習豐田,為什么到現(xiàn)在為止,還沒有任何一個公司能夠像豐田汽車那樣——系統(tǒng)、高效和持續(xù)地提升質量和成本優(yōu)勢?
原因就在于大部分人將學習的重點放在了可以看得見的工具上面。
豐田一次又一次地對朝圣者敞開工廠的大門,但是我可以想象豐田的領導可能一直在搖頭私語:“歡迎你們來參觀,但是為什么你們對某個問題的解決方案如此感興趣?為什么不去研究我們是如何找到這個解決方案的?”
未來是不可預測的,現(xiàn)在采用的解決方案在未來不一定會適用。競爭優(yōu)勢源于組織在現(xiàn)狀的基礎上找到合適的解決方案的能力,并不依賴于解決方案本身——例如精益方法、高利潤的產(chǎn)品等。
舉個例子,很多年前,我的一個朋友參觀了日本的工廠,發(fā)現(xiàn)所有車型的零部件都通過流動式貨架送到工位上。通過這樣方式,操作者可以從貨架上拿到不同車型的零件,從而不需要更換貨架上的零件就實現(xiàn)了混線生產(chǎn)。我們中的很多人復制了這個方法很多年。
不久前,我的這位朋友回到那個工廠,發(fā)現(xiàn)流動式貨架都不見了,取而代之的是另外一種方法。同一輛車的不同零件被放在一個“小車”上,隨著車身在裝配線上往下流動。當車身到達裝配工位時,操作者只看見這些零件,每次也從相同的地方拿取零件。
我的這個朋友有些失望,于是問負責接待的豐田員工:“哪一種方式是正確的,或者說哪個更好?流動式貨架還是成套配送?”豐田的員工沒有明白他的問題,只是這樣回答:“前些年,你到訪我們工廠的時候,我們這條線只生產(chǎn)4種車型?,F(xiàn)在我們在同樣的線上生產(chǎn)8種不同的車型,已經(jīng)不可能在流動式貨架上放置所有車型的零件。”
也就是說,如果我們希望組織能夠基業(yè)長青,那么,如何應對內(nèi)部和外部的變化至關重要,而且進無止境。目標不是贏,而是培養(yǎng)組織的能力——持續(xù)改進、適應和滿足不斷變化的顧客需求。想要保持競爭優(yōu)勢并生存下去,這種持續(xù)地、小步地進化和改進的能力才是最好的保證。
二、要基業(yè)長青,你需要深度認知豐田“改善”套路
在豐田,我將這套組織管理系統(tǒng)稱為“改善”套路。
從20世紀30年代到20世紀80年代,西方的汽車制造商在生產(chǎn)力和工廠流程上的進展微乎其微,基本生產(chǎn)技術似乎在原地踏步。相反,豐田的發(fā)展方式是自我調整的流程改善,通過關注達到目標狀態(tài)所必須要做的事情,培養(yǎng)出有盈利能力的流程、產(chǎn)品和業(yè)務。
豐田意識到,高的機器利用率并不會帶來低成本,只有零件從一個工序不間斷地流到下一個工序,中間沒有任何浪費,才能實現(xiàn)真正的低成本。
也就是說,豐田的“改善”套路是在長遠的方向下運用的,這個方向最終也可能是根本無法實現(xiàn)的理想狀態(tài)。不過,我們通常會在相對短期、更具體的目標或者需要的范圍內(nèi),實踐改善套路。
那么,豐田的“改善”套路是究竟怎么運行的?這5個步驟是你必須要掌握的:
1、目標狀態(tài)是什么?
2、實際情況如何?
3、實現(xiàn)目標的障礙是什么?你目前要解決是哪個?
4、下一步的計劃?(新的PDCA循環(huán))
5、什么時候能夠到現(xiàn)場去觀察已經(jīng)實施的改善?
什么是目標狀態(tài)?
目標指的是結果,而目標狀態(tài)則是如果要達到期望的結果,流程應該怎么運行。
舉個例子,一家工廠曾設定了一個目標,成品庫存不超過一天。于是為了達成目標,大家就削減了庫存。但是以當時裝配流程的生產(chǎn)批量和績效標下,一天的成品庫存太少了,結果就是不停趕貨,大大增加了加急運輸?shù)某杀?。正確的做法,應該放在流程上,而不是庫存上。
只有深入流程內(nèi)部,設目標狀態(tài),然后克服阻礙我們實現(xiàn)目標狀態(tài)的障礙,才能明白我們?yōu)槭裁葱枰敲炊鄮齑妗?/p>
三、要像科學家一樣,塑造一個學習型的組織
如何邁向目標狀態(tài)?
目標狀態(tài)建立后,遺憾的是,我們沒有辦法準確地預測前進的道路,灰色地帶自此產(chǎn)生。而豐田的做法是,像科學家一樣,沿路學習,不斷調整,以小而快的步伐朝著目標狀態(tài)前行。
這種實驗的方法被總結為PDCA循環(huán):
1、計劃(plan):確定你期望去做或者發(fā)生的事情。這就是假設或者預測。
2、執(zhí)行(do):檢驗假設,也就是按照計劃的方式運行流程。通常會在開始的時候小規(guī)模試行,仔細觀察運行的情況。
3、檢查(check):將實際結果和預測做比較。
4、行動(act):把有效的方法標準化,并穩(wěn)定下來,或者重新開始一個PDCA循環(huán)。
由此可見,PDCA是一個實用工具,可以幫助我們通過灰色地帶,達到目標狀態(tài),塑造一個學習型的組織。
舉個例子,假設一個起床上班的流程,目標狀態(tài)是醒來后60分鐘內(nèi)坐到車里準備開車去上班。這個PDCA循環(huán)是這樣的:
計劃:醒來后60分鐘內(nèi)坐到車上(目標狀態(tài));
執(zhí)行:醒來,完成早上的例行公事,坐到車里;
檢查:坐到車里的時候看一下總共花了多少時間;
行動:下一步待定
當我們坐到車里開始檢查早上的例行公事花了多長時間的時候,發(fā)現(xiàn)是64分鐘,超過目標狀態(tài)4分鐘。通過這個流程,我們說不出來早上的例行公事在哪里出了問題,更嚴重的是,任何可以讓我們達到目標狀態(tài)的調整都已經(jīng)為時過晚。
當然,你也可能會馬上提出改善建議,例如把鬧鐘提前4分鐘,或者縮短洗澡時間等。我們想要直接提出對策并實施的沖動是如此強烈,而以成果或者結果為基礎的主流管理系統(tǒng)正是形成這種強烈欲望的溫室。
事實上,這個PDCA的實驗有兩件事情是錯誤的:
1、“檢查”太晚,以至于無法學到有關這個流程的任何有用的東西,也就無法中間調整;
2、這個目標狀態(tài)只明確了結果,也就是說根本不是一個目標狀態(tài)。
歷史告訴我們,很多看似巨大而突然的變化都是緩慢發(fā)展而來的。問題在于我們沒能注意到這些正在發(fā)生的小變化,也沒有認真對待。反之,豐田清楚地指出,沒有什么問題小到不需要回應。一個有意識自我調整的組織,在問題還很小而且容易掌握的時候就能發(fā)現(xiàn)。
回到起床上班這個流程。為了要在更短的周期內(nèi)進行試驗,我們需要一個更詳細的目標狀態(tài)。一般來說,目標狀態(tài)包含以下信息:
1、流程的步驟、順序和時間;
2、流程的特征;
3、流程的衡量指標;
4、結果衡量指標。
也就是說,更加有效的起床上班的目標狀態(tài)應該是這樣的:
接下來,我們就能夠沿路檢查、學習和調整了。如下圖所示,做早餐比計劃時間長了4分鐘。我們不但知道問題出在哪里,也能調整剩下來的步驟,使自己仍然能夠達到60分鐘的目標。
和第一次只有結果指標的實驗相比,第二次加入了流程指標和短的PDCA循環(huán),就像戴上了一幅眼鏡,第一次看清楚實際狀況。難怪有時候經(jīng)理們會惹惱一線操作員:短暫地看一下流程,就設定績效激勵機制,胡亂地給出一些消除浪費的建議,然后扭頭回到辦公室。
當然,在這個案例中,下一步就是更仔細地觀察做早餐這件事情,并問:“是什么事情讓我們無法在7分鐘內(nèi)做完早餐?”
以上就是關于豐田改善套路的簡單總結。當然,這其中還有幾個關鍵點,需要你特別注意:
1、重視現(xiàn)場,掌握現(xiàn)狀。
在豐田,問題解決的核心關注并不是解決方案,而是非常深入地掌握工作系統(tǒng)的第一手現(xiàn)狀,然后合適的解決方案才能信手拈來。
所以,豐田的車間并沒有和IT系統(tǒng)相連,管理會計系統(tǒng)在豐田工廠的現(xiàn)場根本沒有什么地位,因為豐田工廠的領導人不喜歡通過會計報告了解情況,公司教導他們直接去現(xiàn)場觀察實際情況。
2、快速的周期。
一般來說,豐田會培訓你專注于單因素實驗,也就是說,一次處理一個問題,在一個流程上一次只改變一件事情。這可以幫助我們理清因果關系,更了解流程。但如果一個循環(huán)就要耗費很長時間,那步伐就太慢了。
因此,單個的PDCA循環(huán)要盡可能快,有時候一個循環(huán)只要幾分鐘的時間。
與之類似,生產(chǎn)流程的目標狀態(tài)持續(xù)的時間,我的建議是,最長不要超過三個月。如果一個目標狀態(tài)延續(xù)超過三個月,那么需要把它分解為相對容易管理的時間段。而對于那些剛開始學習改善套路的人,最佳的時間周期是一至四周。
四、績效指標管理已過時,實時掌握真實情況才是王道
總之,豐田為什么能夠在完成自我設定的挑戰(zhàn)(目標狀態(tài))上,比其他組織都成功?原因并不是我們經(jīng)常認為的,豐田人更有紀律性或者遇到的問題更少。而是他們更早地發(fā)現(xiàn)流程層次的問題,在問題還微不足道的時候就去了解并采取措施。
現(xiàn)在,許多公司在管理上嚴重依賴結果目標設定、績效報表、以投資回報率為基礎的決策模式,但越來越多的證據(jù)顯示,這種機制無法使組織實現(xiàn)有效改善與調整,從而也無法在激烈的市場競爭中持續(xù)經(jīng)營。
為什么?因為通過績效指標進行遠程管理會忽視和掩蓋小問題,從而錯失了及時調整的機會,久而久之,公司的競爭優(yōu)勢會由此衰落。
如果我們想要一個持續(xù)改善和調整的組織,就應該找到方法,將更多的重心放在實時掌握真實情況的細節(jié)上。豐田的改善套路正擅長于此。它提供了一個方法,讓人們以實證和創(chuàng)造性的方式努力工作,實現(xiàn)那些不那么容易達成的目標。
也就是說,豐田經(jīng)久不衰的成就,并不是因為完美的事前決策或者計劃,而是無數(shù)個朝著目標狀態(tài)前行的PDCA循環(huán),一點一滴地積累了豐田在成本、質量和市場上的地位。
建立生產(chǎn)有序、管理順暢,操作規(guī)范,士氣高昂、高質量、低成本、短交期的作業(yè)現(xiàn)場;
為企業(yè)規(guī)劃設計一套由內(nèi)到外的形象升級,外觀視覺價值體現(xiàn)、內(nèi)在的管理內(nèi)涵體現(xiàn);
全員參與設備管理高產(chǎn)出和低成本運營,提升設備管理能力,維護能力,提高效率
構建班組生產(chǎn)管理體系、循環(huán)評價、人才育成、持續(xù)改善、績效管理、文化養(yǎng)成體系;
提高產(chǎn)品質量、降低生產(chǎn)成本、縮短交期、增加利潤,讓管理更系統(tǒng)科學,執(zhí)行力更強
對工廠的各個組成部分進行合理安排,以提高生產(chǎn)效率、降低成本、優(yōu)化物流、改善工作環(huán)境等