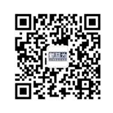
微信公眾號二維碼
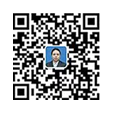
微信咨詢顧問二維碼
精益生產(chǎn)如何消除采購過程中的浪費?新益為精益生產(chǎn)咨詢公司概述:推行精益生產(chǎn)方式,除在制品庫存和成品庫存外,還消除原材料和外購件庫存。消除原材料和外購件的庫存比消除工序間在制品的庫存更難。這是因為,這不僅可以通過企業(yè)內部的努力來實現(xiàn),還取決于供應商。但是購買原材料和零部件占了很多資金,如果不消除這種浪費,推廣精益生產(chǎn)方式的效果就會受損。因此,有必要消除采購中的浪費。
精益生產(chǎn)咨詢
1、消除不必要的工作
精益生產(chǎn)者認為“不能產(chǎn)生價值的工作就是浪費”。一般企業(yè)的采購中有大量活動是不增加產(chǎn)品價值的,如訂貨、改訂、收貨、開票、裝卸、運輸、品質檢查、入庫、點數(shù)、運轉、送貨,等等,都不增加產(chǎn)品的價值。也許有人要問,我不“訂貨”如何生產(chǎn)?
“訂貨”怎能算是浪費呢?且慢,如果通過流程再造或采購方式的改進,“訂貨”作業(yè)的時間從2小時減為10分鐘,那1小時50分不是浪費是什么?準時采購的目的就是要消除“不產(chǎn)生價值”的浪費,消除原材料與外購零部件的庫存。
如何消除這些浪費?應該先從供貨品質抓起。如果供貨品質可以保證,就可以取消購入檢查。有人認為取消購入檢查會增加風險,事實證明,推行精益生產(chǎn)方式減少了品質不合格的風險。
2、與供應商建立新型伙伴關系
對于傳統(tǒng)的大批量生產(chǎn),組裝廠與零件供應廠之間是一種主仆關系。當組裝廠的一種新產(chǎn)品的零件圖出來之后,才開始選擇供應廠家。選擇的標準是在供應廠家保證達到設計要求并按期交貨的前提下,價低者勝出。在大批量生產(chǎn)方式下,汽車組裝廠的供應商數(shù)通常為1000-2500個。由于供應商不了解整個產(chǎn)品,甚至也不了解與它們制造的零件相關的零部件,它們通常不知如何保證整個產(chǎn)品品質,也不知從何處改進。多個供應商生產(chǎn)的零件因工差關系容易造成組裝上的困難。更重要的是,供應商也沒有改進工作的積極性。組裝廠為了獲取更多利潤,采取讓供應商之間競爭的辦法來降低成本。在利潤分配上,絕大部分利潤歸組裝廠,供應商不僅得利很少,而且還可能像一個雇工一樣被解雇。因此,它們沒有長期合作的打算,也沒有改進品質的積極性。
精益生產(chǎn)方式下,為了消除采購中的浪費,選擇盡量少的、合格的供應商。選擇盡量少的供應商,是因為企業(yè)的力量和資源有限,只能幫助較少的供應廠家去消除浪費,組織好準時生產(chǎn)。
面對成千個供應廠家,企業(yè)是分身乏術的。因此,要同供應商建立不同以往“主仆關系”的新型關系。這種關系應該是長期的、互利的。
因為只有建立長期的關系,才便于解決品質問題;只有基于“雙贏”,才能建立長期的合作關系。合格的供應商具有較好的設備、技術條件和較好的管理水平,可以保證準時供貨、保證品質。供應商是從合作共事過的企業(yè)中挑選的。在新產(chǎn)品開發(fā)初期,供應商就可以參加進來。按承擔的任務不同,將供應商按不同層次組織起來。組裝廠只與一層供應商直接發(fā)生聯(lián)系。一層供應商一般承包一個獨立的部件的設計與制造。一層供應商根據(jù)需要再將該部件下的零件給二層供應商承包。依此類推。
這樣,組裝廠只需同較少的供應商直接打交道。日本的汽車制造廠的供應商一般只有300家左右。
在確定零部件價格時,裝配廠按市場行情確定汽車目標價格,與供應商一起考慮合理利潤,估算各部分目標成本。為了實現(xiàn)目標成本,雙方共同利用有價值的工程方法,逐一找出可以降低成本的要素。然后一樓的供應商與組裝廠商量,如何實現(xiàn)目標成本,給供應商帶來合理的利潤。在零件的生產(chǎn)過程中,復用通過分析加工制造的各個步驟,進一步降低成本。供應商之所以能積極降低成本,是因為降低成本能帶來更多的利潤。
在選擇供應商時必須考慮四個核心因素:經(jīng)營能力、技術競爭力、質量管理和內部生產(chǎn)管理能力、地理位置和價格。放下價格后,可以在現(xiàn)在三個條件都具備的時候討論價格,而不是價格不重要。此外,往往前三個因素較好的供應商,價格也可能較低。否則,雙方建立合作關系后,企業(yè)可以幫助供應商實施精益生產(chǎn)方式,找到降低成本的方法,降低價格。建立良好的合作關系后,可以簡化和消除訂貨、修改訂貨、質量檢查等多項工作,減少浪費。
精益生產(chǎn)如何消除采購過程中的浪費?以上就是新益為精益生產(chǎn)咨詢公司的相關介紹,做好企業(yè)的精益生產(chǎn)管理工作就是為精益管理活動打下基礎,讓精益管理在企業(yè)中發(fā)展有一個良好的前提。
文章來源于網(wǎng)絡,版權歸作者所有,如有侵權請聯(lián)系刪除!
建立生產(chǎn)有序、管理順暢,操作規(guī)范,士氣高昂、高質量、低成本、短交期的作業(yè)現(xiàn)場;
為企業(yè)規(guī)劃設計一套由內到外的形象升級,外觀視覺價值體現(xiàn)、內在的管理內涵體現(xiàn);
全員參與設備管理高產(chǎn)出和低成本運營,提升設備管理能力,維護能力,提高效率
構建班組生產(chǎn)管理體系、循環(huán)評價、人才育成、持續(xù)改善、績效管理、文化養(yǎng)成體系;
提高產(chǎn)品質量、降低生產(chǎn)成本、縮短交期、增加利潤,讓管理更系統(tǒng)科學,執(zhí)行力更強
對工廠的各個組成部分進行合理安排,以提高生產(chǎn)效率、降低成本、優(yōu)化物流、改善工作環(huán)境等